Description: 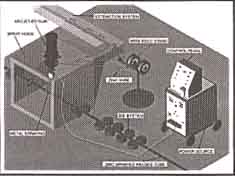
Arc spray is the most userfriendly, and in terms of operating cost, the least expensive of the thermal or metal spraying processes based for applying metal coatings on base materials. Any electrically conductive material in wire form can be arc sprayed. A wire feeder pushes two electrically charged metallising wires to the gun. The wires meet at the head of the gun and melt in the electric arc. The molten mass is atomised and blown onto the substrate with compressed air. The particles cool to ambient temperature and coalesce into a high quality metal coating. A roll-forming machine draws hot or cold rolled steel through successive stations and shapes the material into a tube. Electric resistance welding closes the seam left by the butted edges. Although no filler metal is added that would change the chemical composition, the welding process applies temperatures high enough to sacrifice some corrosion-resistant properties of the base metal. The process may also vaporize aluminum or galvanized coating previously applied to the rolled steel. A contoured/scraping tool or smoothing mandrel removes weld spatter or excess material from the outer diameter of the tube surface. Many tube makers install a two-wire electric arc spray process directly down line from the scraping tool or smoothing mandrel. Applying the spray material while the weld seam is still hot assures a metallurgical bond of the sprayed material with the substrate, improves both the deposit efficiency and density of the sprayed material and allows the coating to blend.